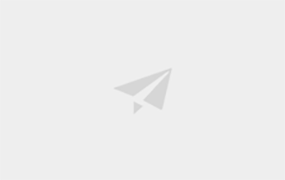
四川启明星铝业有限责任公司成立于2001年12月,是按现代企业制度投资组建,高起点、高标准建设。于2003年9月29日建成投产,现已形成25万吨电解铝及19万吨阳极产能。项目采用了多项国际、国内领先的技术,引进了国际先进设备15项倾力打造的企业核心竞争力。在现代化的企业管理中,如何把握现代企业的发展趋势,结合具体情况探索设备管理的基本原理和方法,建立一套实用、高效的设备管理体系,对提升企业设备管理水平,增强企业竟争能力,提高企业经济效益具有重要现实意义。
在10年多的设备管理工作中,通过我们坚持不懈的探索,以状态检测、点检、计划维修为基础的预知维修模式。建立、并不断完善设备管理体系过程中,管理技术水平逐年提高。这套设备管理系统制度在建立、执行和不断完善过程中,设备维修策略有些不尽科学的地方,需要认真的思考和总结,例如:因设备突发故障而进行停机修理 。严重时引起生产中断 ,打乱生产计划 ,使企业的生产活动不能正常进行 ,带来一定的经济损失。特别是在生产作业连续性很强的车间里如:成型、组装、电解、铸造等车间。下面从我公司设备状况、优化原则、夯实“全员”设备管理基础深入开展预知维修的经验如下:
管理经验总结如下:
1 目前公司设备管理现状
我厂在设备维修管理的组织形式上,采用生产车间、检修车间、设备动力部、设备厂长的四级管理模式。对设备点检及状态监测的定义,主要指按照设备的运行标准,对重点、关键部位的运行状态进行检测管理,使设备的异常状况和劣化趋势能够在故障早期被发现。我们的设备检修、维护则以此为基础开展、指导。
(1)各车间根据公司设备管理思路、规划,结合车间设备特点 ,相继开展设备的日常点检为基础的设备维护、保养工作。依靠生产操作工人的感官对设备定期进行检查 ,发现问题及时联系检修车间人员采取维修措施;检修车间利用专用检测工具对各车间设备按计划定时、定人进行专业点检、状态监测,各专业工程师对结果进行分析、处理,根据结果决定是否安排检修工作。设备动力部对生间车间和检修车间设备管理工作进行监督管理。
(2)对公司设备管理理念,员工普遍认识不足,同时最初制定的设备的检测部位、检测标准、检测方法,主要依据经验制定。因此员工缺乏自主、主动参与的积极性。设备管理中存在漏项、缺项标准不适用、方法原始等问题。
(3)对设备点检及状态监测形成的数据,处理机制不完善。对设备工作的维护检修不具有指导作用。生产车间点检及状态监测数据没有有效与检修车间专业性点检进行结合。
(4)专业点检及状态监测工作主要由检修车间承担,按计划安排具有一定相应专业能力人员 ,对全厂设备关键部位的各种参数(温度、振动)采用专用仪器进行检测、记录汇总。没有充分利用特征参数的检测结果,描述设备劣化程度的。对设备维修及维护没有起到及时的指导作用。
2 夯实“全员”设备管理基础,优化设备管理工作
要提升企业管理水平,增强企业竟争力,提高企业经济效益。必须进一步提高“全员”设备管理水平,针对性的采取以下措施,大力提倡设备管理工作的“标准化、规范化”夯实管理基础工作:
(1)清理、完善设备管理制度,完善相关紧急预案及流程、设备运行状态、设备维修、设备润滑和设备点检等技术标准;完善设备综合管理评价体系。使设备管理体系有效运行,有章可循、行有规范
(2)加强通过宣传、培训、引导工作,让全员设备管理思想在公司员工脑海中扎根。在员工的积极参与之下,使得设备维修管理的全过程及各个环节的行为规范化、流程闭环化、控制严密化、精细化和标准化的设备管理,在设备检修、维护过程中能够彻底执行。
(3)建立以状态监测及点检制度的流程为基础的设备维修体系。对流程进行疏理,主要清理流程不畅、去繁存精、加强弱点,去除功能重复以提高运行效率为原则。
(4)建立、完善设备零缺陷管理体系,专业管理与群众管理相结合、设备标准化操作与设备运行相结合、设备维护与设备点检相结合,检修质量与生产相结合,规范设备缺陷管理的流程和考核,实现设备运行、维修的“零缺陷”,确保设备安全、高效稳定运行。
(5)设备管理规范化、标准化。根据企业的设备要求 ,制定、完善可以指导操作、维修及生产人员可以参加的设备管理制度及技术维护、检修标准及奖罚制度。做到真正的“全员”设备管理,在设备管理各个环节中做到,有 “法”可依 ,有“法”必依、违法必究的理念。
(6)对不同岗位工人的操作范围及点检部位进行界定,同时加强对设备临检故障的终端控制。以科学的、实事求是的态度,组织相关技术人员对设备故障进行认真分解、分析 ;根据情况修正相应的点检、状态监测,并制定、调整相关的培训计划、维修、维护计划。定期组织员工进行交互式培交流,对较大、较难问题,可视情况成立QC技术骨干小组,针对性的性解决问题。
(7)利用信息化工具建立点检及状态监测专业数据库,绘制设备劣化趋势图,根据设备技术标准,利用该图来分析、判断设备的劣化程度。 高效、有的放矢开展设备点检定修,及时采取维修措施。同时可实现数据共享,有利于车间及设备管理部门的设备管理,并可作为设备管理好坏评价的参考依据。
(8)确定明确的操作范围与对象,即要解决做什么的的问题,指在操作范围上进行一定界定。主要目标清理设备管理死角,防止三不管设备出现。专业检修人员做什么,设备维护人员需要做什么。如在设备维护上操作范围,即需要确定进行清洁、点检、润滑保养的部位、内容、周期等。
(9)必须确定不同设备检测内容和标准,即要解决怎么做,达到什么目的的问题。根据所选“点”的特点 ,必须进行的若干项内容实施,对每一点的每一项操作内容制定相应的目标状态或标准。
(10)确定合理的点检及状态监测合理的运行模式,即要解决如何高效的做的问题,如成型车间已实施的每班定点巡检路线。相关单位可以根据设备布局及工艺流程对所选的操作点按照一定的原则制定 ,例如:可以画出点到点的连线 ,优化出一条较短、较易、较省力气的点检及状态监测示意图,并上墙。
(11)建立完善生产车间“日常点检”、“ 周点检”,检修车间“专业点、状态监测”相结合制度,并进行“每月设备点检、状态监测综合分析”,对设备运行实现全面、主动、适时、预知的点检模式,及时准确在点检中掌握设备状态。
多年以来,我公司的设备管理工作以“全员”设备管理理念为指导,探索以状态检测、点检、计划维修为基础的预知维修模式。从设备管理体系建立、完善取得了丰富的经验。其核心内容是“全员”预防维修,基础是设备点检及状态监测的标准化、规范化,目的是通过有效的组织和技术管理 ,准确实时掌握设备运行技术状态信息 ,实现以预防为主的设备维修管理,大量地减少设备故障和事故,减少设备维修工作量。逐步从周期计划预修过渡到按设备状态的预知维修 ,提高设备维管理水平 ,降低设备运行成本。